What Is Inventory Management? Process, Challenges & Solutions
.png)
Imagine having the power to know exactly what’s in your warehouse at any given moment, ensuring that your customers always find what they need—no more empty shelves or overstocked items. Effective inventory management is the secret ingredient that transforms a chaotic stockroom into a well-oiled machine.
Consider this: companies that streamline their inventory processes can cut operational costs by up to 10%, while nearly 42% of businesses lose revenue each year due to poor stock management. These figures highlight how crucial a smart inventory system is—not just for efficiency, but for driving growth and customer satisfaction.
In this guide, we’ll explore the ins and outs of inventory management, from the basics to advanced techniques, and share practical tips that will help you harness the full potential of your inventory. Whether you’re a small business owner or part of a larger enterprise, get ready to unlock strategies that will keep your stock organized, your costs down, and your customers happy.
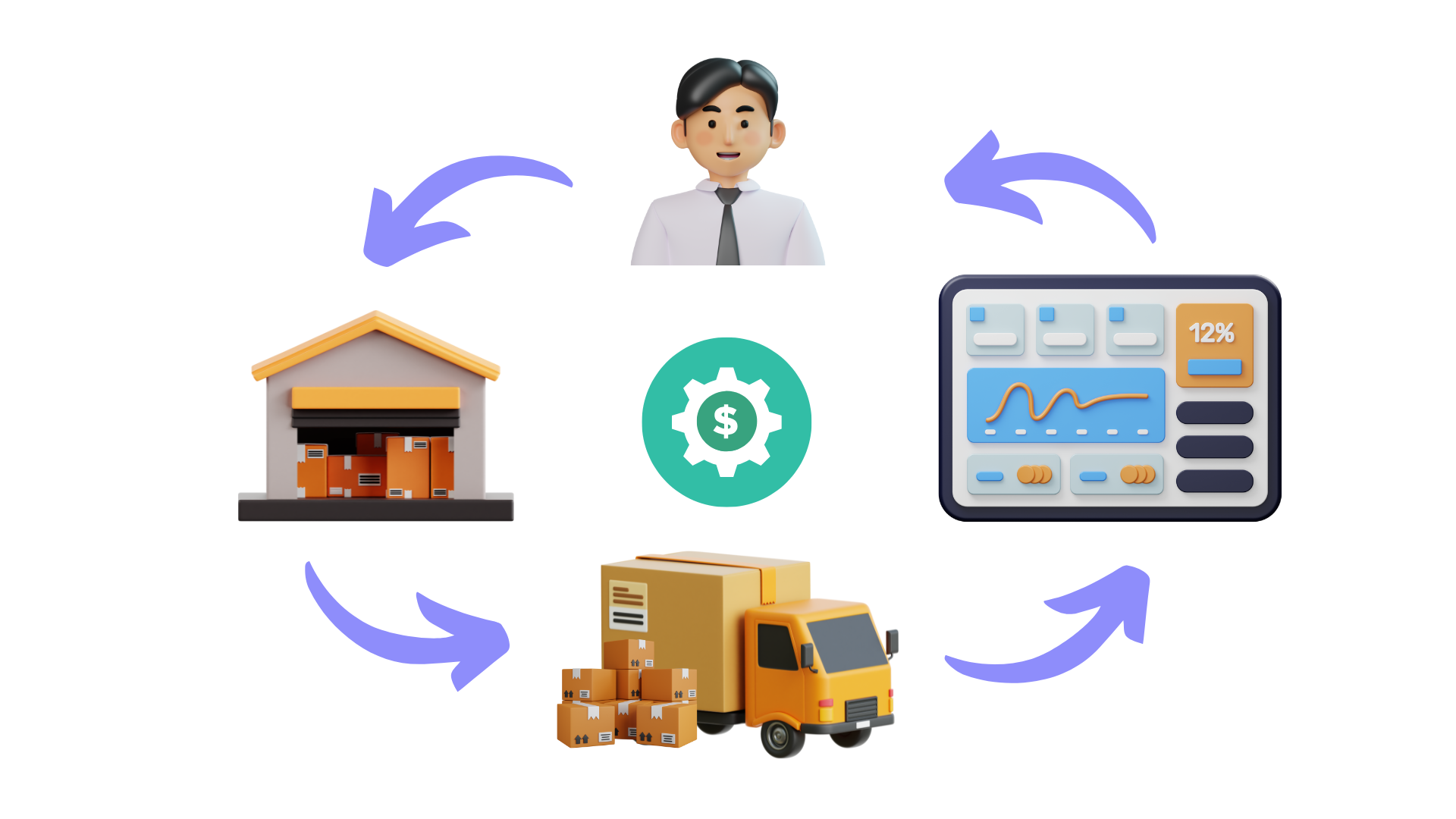
What is Inventory Management?
Inventory management is the process of monitoring and organizing your stock so that you always know what you have and when to reorder. It’s about striking the perfect balance—ensuring you have enough items to meet customer demand without tying up too much cash in excess stock
At its core, it's about balancing supply and demand to avoid overstocking or running out of items. Think of it as managing a kitchen pantry: you want enough ingredients for your recipes, but not so many that they spoil.
For example, if you own a small bookstore, inventory management helps you track the number of copies of each book, know which titles are selling fast, and reorder them before your shelves run empty. It’s a continuous process that involves forecasting demand, ordering supplies, and monitoring stock levels to keep everything running smoothly.
What is an Inventory Management System?
An inventory management system is the tool—or software—that brings efficiency and precision to the inventory management process. Rather than manually counting items or scribbling notes on a notepad, this system automates the tracking of inventory in real time.
It provides features like barcode scanning, automated reorder alerts, and detailed reporting, making it easier for businesses to maintain optimal stock levels. Imagine running a restaurant where ingredients are ordered through a smart system that tracks usage and alerts you when it’s time to restock; that’s the power of an inventory management system. It not only saves time but also minimizes errors, helping you make informed decisions and streamline operations.
Both inventory management and its supporting systems play a vital role in ensuring that your business operates efficiently, reduces costs, and keeps your customers happy with reliable product availability.
Why Is Inventory Management Important?
Inventory management isn’t just about keeping track of items—it’s a strategic practice that can fundamentally change the way your business meets customer demands and navigates market shifts. Here are several concrete benefits that illustrate why a robust inventory management approach is essential:
- Enhanced Stock Visibility:
With up-to-the-minute insights into your inventory, you can monitor exactly what is available at any given moment. This clarity helps you identify trends and seasonal patterns, allowing for more precise stock levels and ensuring that critical items are always visible in your system. - Optimized Reordering:
Detailed tracking data empowers you to pinpoint the optimal moment to reorder products. This proactive approach minimizes both surplus stock and potential shortages. You can tailor reordering strategies to match real-world demand fluctuations, which means your stock levels reflect what your customers actually need. - Improved Product Rotation:
By closely monitoring the lifecycle of each product, you can ensure that older items are moved before they lose appeal. This not only prevents obsolescence but also keeps your offerings fresh and aligned with current trends. Effective rotation also reduces the risk of markdowns due to stale inventory. - Minimized Stock-Outs:
Reliable forecasting and real-time monitoring mean you can predict when popular items are likely to run low. This proactive insight allows you to replenish stock before a critical shortage occurs, ensuring your customers find what they’re looking for without delay, thus protecting your reputation. - Streamlined Operations:
Automation and accurate record-keeping reduce the complexity of manual inventory checks. With a more organized system, you can eliminate discrepancies and focus on fine-tuning your processes. This structured approach ensures that your operations are running smoothly, from receiving shipments to fulfilling orders. - Stronger Supplier Relationships:
Having detailed inventory data fosters transparent communication with suppliers. When you have precise figures on product turnover and demand, you can negotiate better terms and delivery schedules. This reliability benefits both parties, resulting in more synchronized and efficient supply chain operations. - Actionable Insights:
In-depth reporting on inventory trends, turnover rates, and seasonal fluctuations offers a goldmine of information. These insights enable you to refine purchasing strategies, adjust product mixes, and even tailor marketing efforts. By acting on this data, you position your business to adapt more quickly to changing market conditions.
Improved Customer Satisfaction
With a robust inventory management process in place, you can ensure that popular items are consistently in stock. This reliability not only enhances the shopping experience but also builds trust with your customers, leading to stronger loyalty and positive word-of-mouth.
Inventory Management Process
The inventory management process is a series of well-coordinated steps designed to ensure that your stock levels accurately match customer demand, while also optimizing your operational efficiency. Here’s a closer look at each stage of the process:
1. Planning and Forecasting:
This initial phase is all about predicting future demand. You analyze historical sales data, market trends, and seasonal fluctuations to forecast which products will be in demand. By setting realistic inventory targets, you create a roadmap that guides your purchasing decisions and prevents both overstocking and shortages.
2. Procurement and Replenishment:
Once you have a clear forecast, the next step is to procure the right quantities from your suppliers. This involves negotiating terms, scheduling deliveries, and placing orders at the optimal time. Effective procurement ensures that you’re not holding excess stock while also guaranteeing that popular items are replenished promptly.
3. Storage and Handling:
After goods arrive, proper storage is essential to maintain their quality and accessibility. This phase focuses on organizing your warehouse or store so that items are easy to locate and manage. Efficient storage solutions—whether it’s shelving systems, climate control, or inventory categorization—help reduce the risk of damage and make stock-taking more efficient.
4. Tracking and Monitoring:
Real-time tracking is a critical part of the process. Using tools like barcode scanning or RFID tagging, you can monitor the movement of items as they come in and go out. This constant monitoring not only helps you know your current stock levels but also flags any discrepancies early, ensuring accuracy in your records.
5. Analysis and Reporting:
The final phase involves evaluating the entire inventory cycle. Detailed reports and performance metrics, such as turnover rates and stock-out frequencies, provide insights into what’s working and what needs adjustment. By analyzing this data, you can refine your forecasting methods, improve your procurement strategies, and ultimately enhance the overall efficiency of your inventory system.
Inventory Management Techniques and Methods
- Just-in-Time (JIT):
This technique minimizes inventory levels by aligning deliveries closely with production schedules. By receiving goods only when needed, JIT reduces storage costs and limits waste, though it requires robust supplier relationships and reliable transportation. - ABC Analysis:
Not every item in your inventory carries the same value. ABC Analysis segments stock into three categories—A, B, and C—based on factors like cost, usage rate, and turnover. This method lets you focus resources on high-priority items while managing lower-value stock with less intensive controls. - Economic Order Quantity (EOQ):
EOQ is a mathematical model that calculates the ideal order size to minimize both ordering and holding costs. By understanding the trade-off between these expenses, you can order just the right amount to optimize overall cost efficiency. - Safety Stock:
This method involves keeping a buffer of extra inventory to safeguard against unexpected demand spikes or supply delays. Safety stock acts as insurance, ensuring that your operations continue smoothly even when forecasts are off. - Reorder Point (ROP):
Calculating the exact level of inventory at which you need to place a new order is critical. The reorder point is determined by lead time and average demand, ensuring that you replenish stock before it dips too low. - Demand Forecasting:
Using historical data, market trends, and seasonal patterns, demand forecasting predicts future sales. This data-driven approach helps you plan for fluctuations and make informed purchasing decisions, reducing the risk of overstocking or stockouts. - Vendor Managed Inventory (VMI):
In VMI, suppliers take charge of managing their products at your location. This collaborative method not only improves replenishment efficiency but also strengthens supplier partnerships, as both parties share critical sales and inventory data. - Batch Tracking:
By tracking products in batches, you can monitor the performance and quality of specific production runs. Batch tracking is essential in industries where traceability is crucial, such as in regulated sectors or when dealing with perishable goods. - FIFO (First In, First Out):
FIFO ensures that the oldest inventory is used or sold first, reducing the likelihood of items becoming obsolete or expiring. This approach is particularly important for perishable items and products with a limited shelf life. - LIFO (Last In, First Out):
In contrast to FIFO, LIFO assumes that the most recently acquired stock is used first. While less common in industries with perishable goods, LIFO can be beneficial in environments where costs are rising, although it does come with specific accounting and tax implications. - Perpetual Inventory Systems:
These systems continuously update your inventory records with each sale or purchase. With real-time data at your fingertips, you can make prompt decisions, track discrepancies, and maintain a dynamic overview of your stock levels. - Periodic Inventory Systems:
Instead of constant updates, periodic systems count inventory at set intervals. While this method might be less accurate in rapidly changing environments, it can work well for businesses with slower turnover rates. - Consignment Inventory:
In a consignment setup, suppliers retain ownership of inventory stored at your location until it’s sold. This approach reduces your capital investment while ensuring that you have a ready supply of products without taking on the full financial risk. - Kanban System:
Originating from lean manufacturing, the Kanban system uses visual signals—often cards or digital prompts—to trigger inventory replenishment. This method creates a pull-based system where restocking happens only as needed, thereby reducing excess inventory. - Cycle Counting:
Instead of a full-scale inventory count, cycle counting involves regularly scheduled counts of selected items. This continuous auditing process helps identify discrepancies and maintain accurate records without disrupting daily operations.
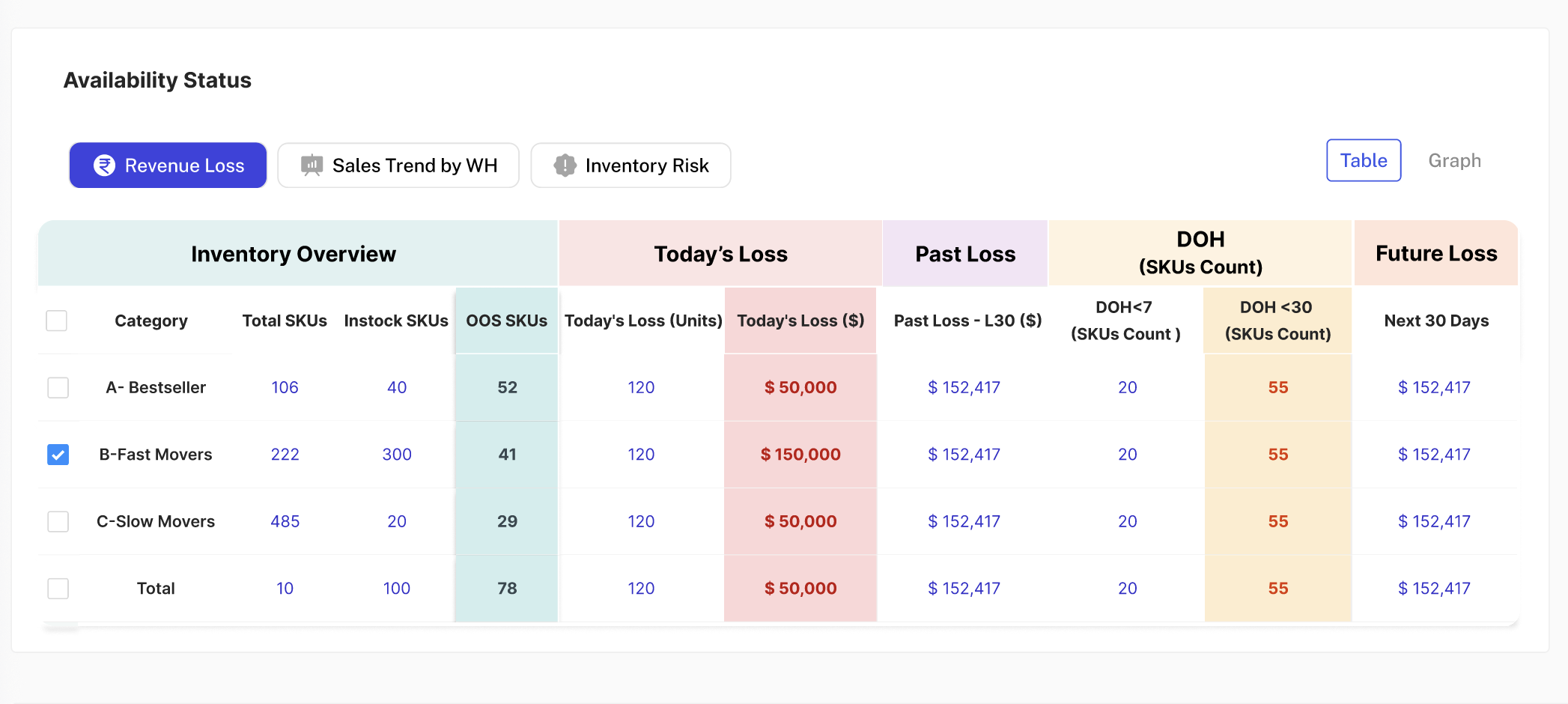
What is Multi-Location Inventory Management?
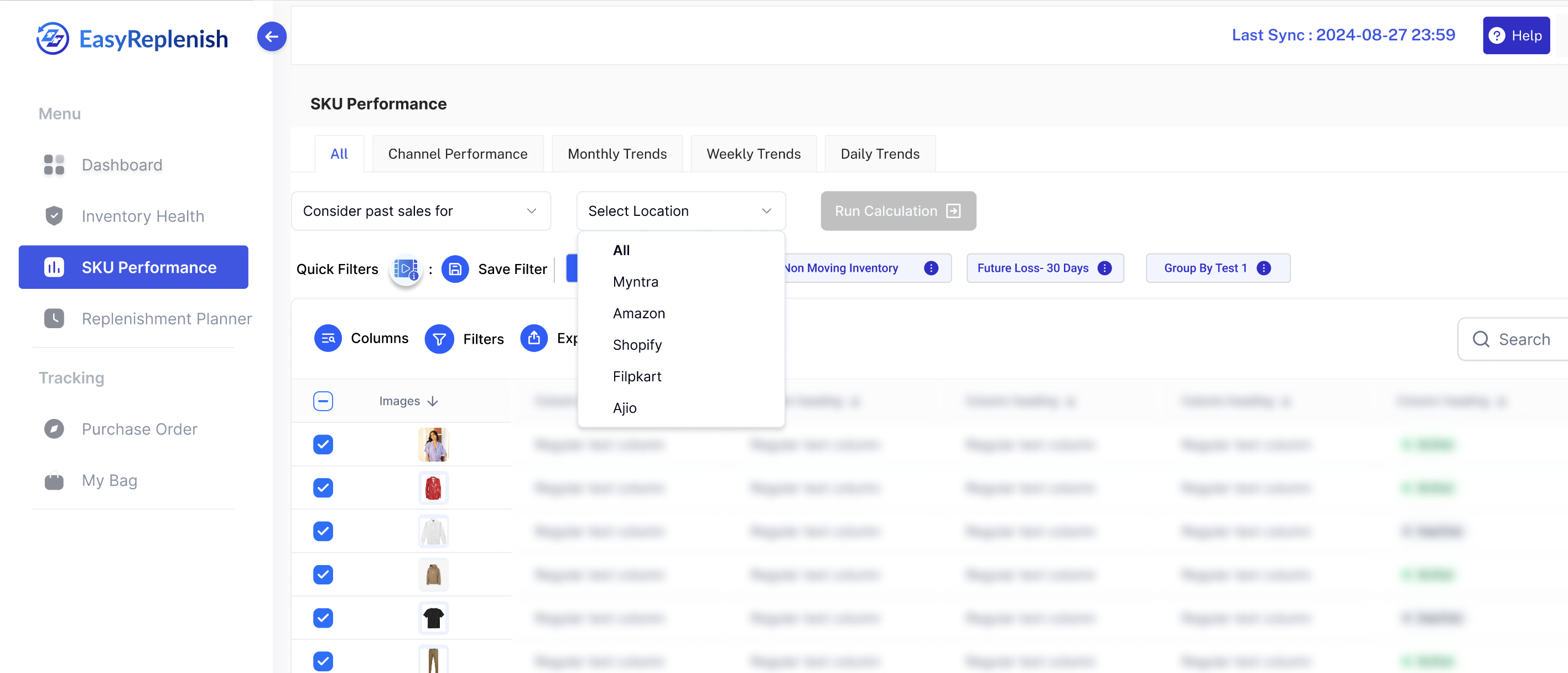
Multi-location inventory management refers to the coordinated process of overseeing stock distributed across several sites—whether they are multiple warehouses, retail outlets, or regional distribution centers. This approach ensures that each location has the right products, quantities, and visibility, all while maintaining a central overview for streamlined decision-making.
At its core, multi-location management tackles the complexity of tracking and balancing inventory across diverse physical spaces. It involves harmonizing data from various sources, so you always have a clear picture of stock levels, regardless of where items are stored. This centralized view allows businesses to strategically allocate resources, transfer stock between locations, and optimize distribution based on regional demand.
Key aspects include:
- Centralized Data Integration: Consolidates inventory information from all locations into one accessible platform, ensuring real-time updates and consistent reporting.
- Stock Reallocation: Enables dynamic transfers between sites to address demand spikes or correct imbalances, reducing the risk of overstock in one location and stock-outs in another.
- Regional Demand Analysis: Empowers businesses to analyze trends and sales performance by region, allowing tailored stocking strategies and more precise forecasting.
- Improved Customer Service: By ensuring the right products are available at the right locations, multi-location inventory management helps enhance customer satisfaction and reduces delays in order fulfillment.
- Cost Efficiency: Optimizes storage and transportation costs by determining the most effective inventory distribution and minimizing excess stock at any one site.
Overall, effective multi-location inventory management is a strategic tool that not only simplifies the operational complexities of handling inventory across various locations but also drives improved responsiveness to market demands and customer expectations
How is Inventory Management Different From Other Inventory Activities?
1. Inventory Management vs. Inventory Control
Inventory management is the overarching strategy that encompasses planning, ordering, and maintaining optimal stock levels. It looks at the whole lifecycle of inventory—from procurement to turnover—ensuring that the right products are available at the right time. In contrast, inventory control zooms in on the day-to-day operations, focusing on the accurate tracking and recording of items. While management is about strategy and decision-making, control is about execution and maintaining precise records.
2. Inventory Management vs. Inventory Optimization
Inventory management provides the framework for handling stock, but inventory optimization dives deeper into fine-tuning that framework. Optimization involves analyzing data, setting parameters, and using techniques (like EOQ or safety stock calculations) to achieve the most cost-effective balance between supply and demand. Essentially, while management sets the direction, optimization refines the process to ensure minimal waste and maximum efficiency.
5. Inventory Management vs. Warehouse Management
Although both functions deal with inventory, warehouse management is primarily concerned with the physical handling, storage, and movement of products within a facility. Inventory management, on the other hand, encompasses broader considerations including procurement, forecasting, and supplier relationships. Warehouse management focuses on logistics—ensuring that items are stored properly, retrieved quickly, and handled safely—whereas inventory management is about aligning stock levels with overall business strategy.
4. Inventory Management vs. Demand Forecasting
Demand forecasting is a critical component of inventory management but is only one piece of the puzzle. It involves predicting future sales based on historical data, market trends, and seasonal patterns, which informs how much inventory to order. Inventory management takes these forecasts and combines them with procurement, storage, and sales data to make holistic decisions. In short, forecasting is about anticipating demand, while inventory management uses that insight to ensure the entire supply chain is responsive and efficient.
Conclusion:
This guide has taken you on a journey through the essentials and nuances of inventory management. We've defined its role in balancing stock with customer demand, explored the benefits of automated inventory systems, and detailed every step—from forecasting and procurement to storage, tracking, and analysis.
We also delved into advanced techniques like JIT, ABC analysis, and cycle counting, and clarified how inventory management differs from related processes such as inventory control, optimization, warehouse management, and demand forecasting.
Ultimately, the insights provided here serve as a roadmap to help you build a more responsive, efficient, and strategic inventory system that drives business growth.
Optimize Your Inventory Effortlessly
Receive timely insights and updates to ensure your inventory stays perfectly aligned with demand.
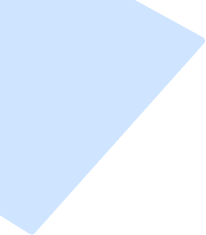
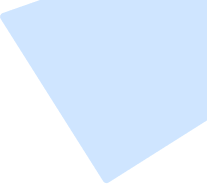
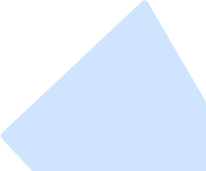
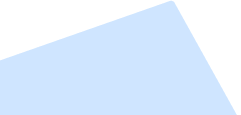