How Offduty Improved Availability & Reduced Stockouts with Smarter Inventory Planning
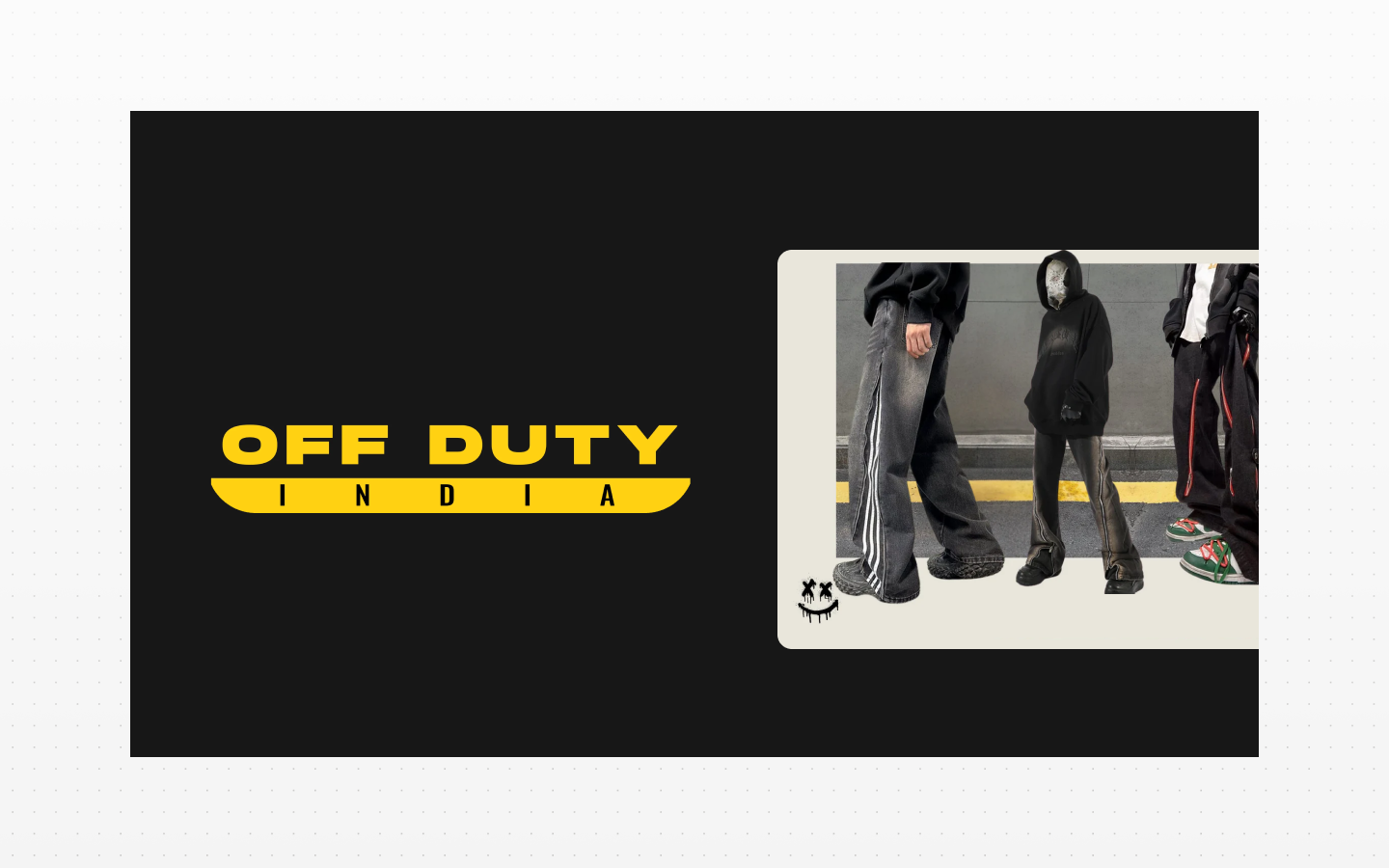
About Offduty
Offduty is a fast-growing fashion brand known for its trendy apparel. As the brand scaled, managing stock availability, reducing stockouts, and optimizing inventory became critical challenges.
Challenges Faced
- Bestseller Stockouts: Low bestsellers availability levels
- Stockout Visibility Issues: Lack of tracking for Segment A Out-of-Stock (OOS) days, impacting revenue.
- Manual Reorder Planning: Slow and inefficient replenishment process.
- Fragmented Team Operations: Founder and inventory planning manager lacked a shared system for stock decisions.
- Surplus Inventory Build-up: C and D category inventory remained high, blocking capital.
Solution Implemented
- Stockouts: Bestseller stockouts reduced by 19%
- OOS Days Comparison for Growth: Measured Segment A OOS days before and after implementation, highlighting topline impact.
- One-Click Reorder Planning: Automated restocking decisions for faster execution.
- Unified Software for Teams: Founder and inventory manager accessed real-time data on a single platform.
- C and D category inventory reduced by 18% in four months, freeing up working capital.
Results
- Stockouts: Bestseller stockouts reduced by 19%
- Revenue Growth: Reduced OOS days for Segment A, directly improving topline.
- Faster Reorder Execution: Automated planning reduced restocking delays.
- Lower Surplus Inventory: 18% reduction in C and D category stock, optimizing cash flow.
EasyReplenish enabled Offduty to increase availability, reduce stockouts, and optimize inventory while lowering excess stock.
5 step guide to optimise your inventory
Get your free copy now.
Optimize Your Inventory Effortlessly
Receive timely insights and updates to ensure your inventory stays perfectly aligned with demand.
Thank you! Your submission has been received!
Oops! Something went wrong while submitting the form.
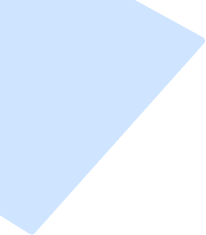
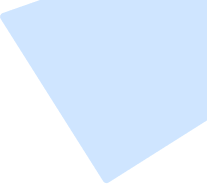
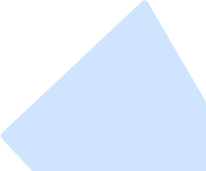
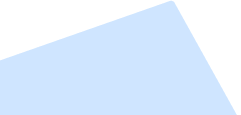